Building things ain’t easy. Building them to tight tolerances can be down right hard. This little gem is a rudder component to the Defiant air frame. The customer requested tolerances of 0.005 inch on a few critical dimensions. We did that and held it pretty tight on the rest.
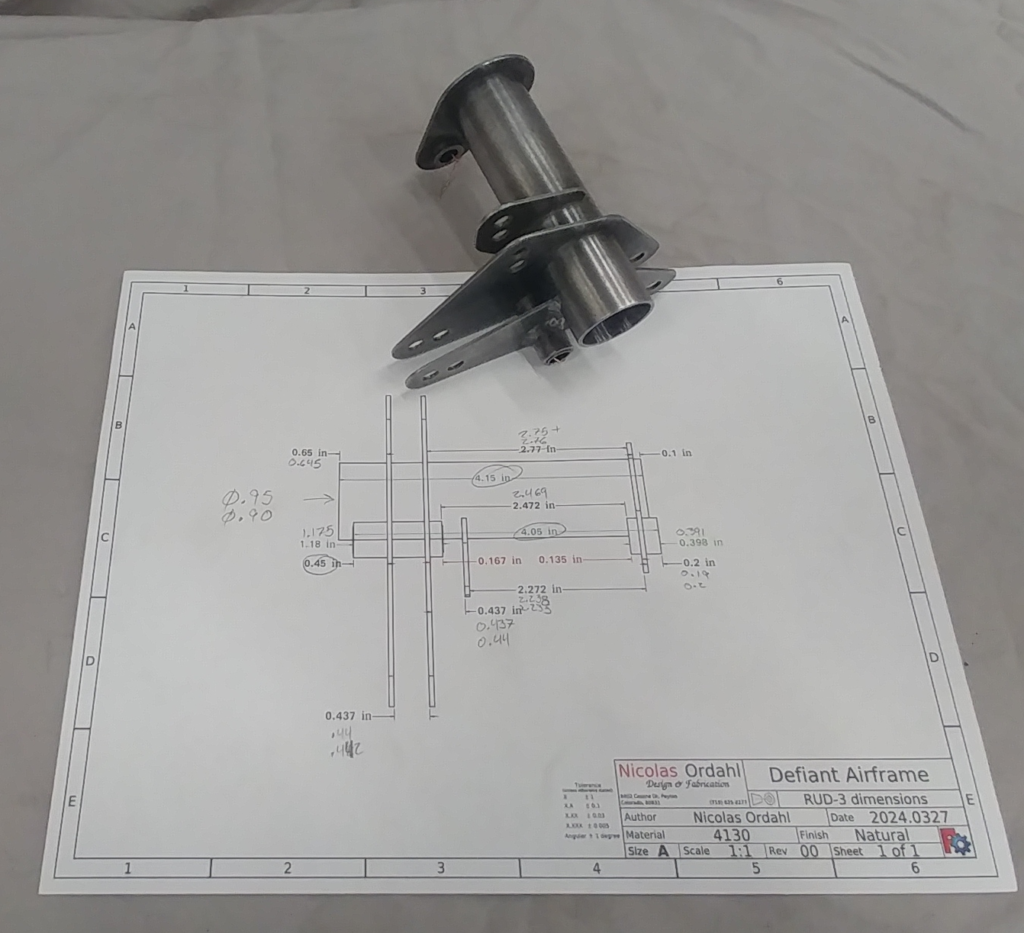
Using one of our 3D printers we created several spacers to hold the tubes in position and the sheet metal components at the required distances. Assembly still took many hours, and to maintain perfect parallel dimensions the small tube was cut and finished after it had been completely welded, no margin for error on that stage.
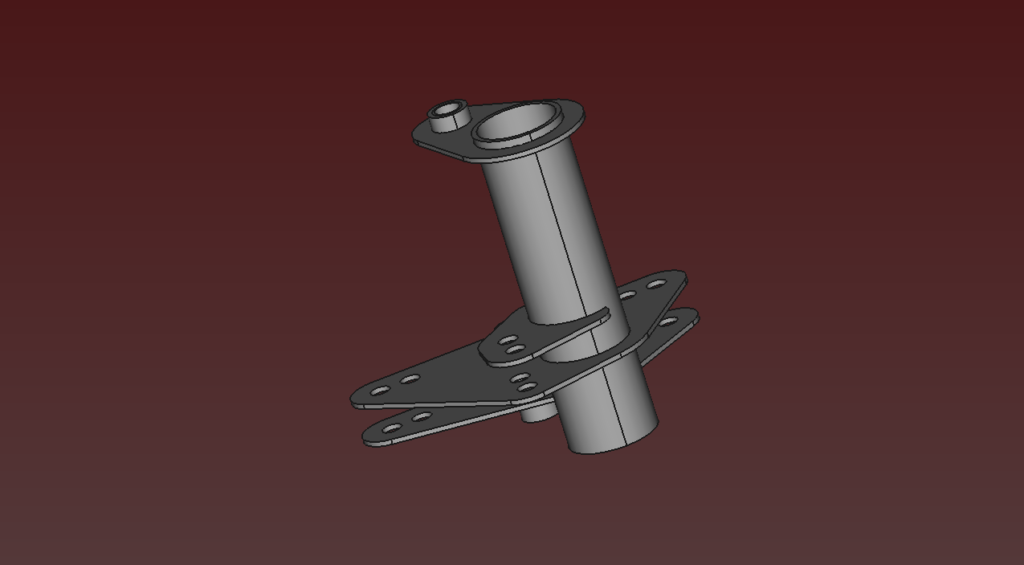
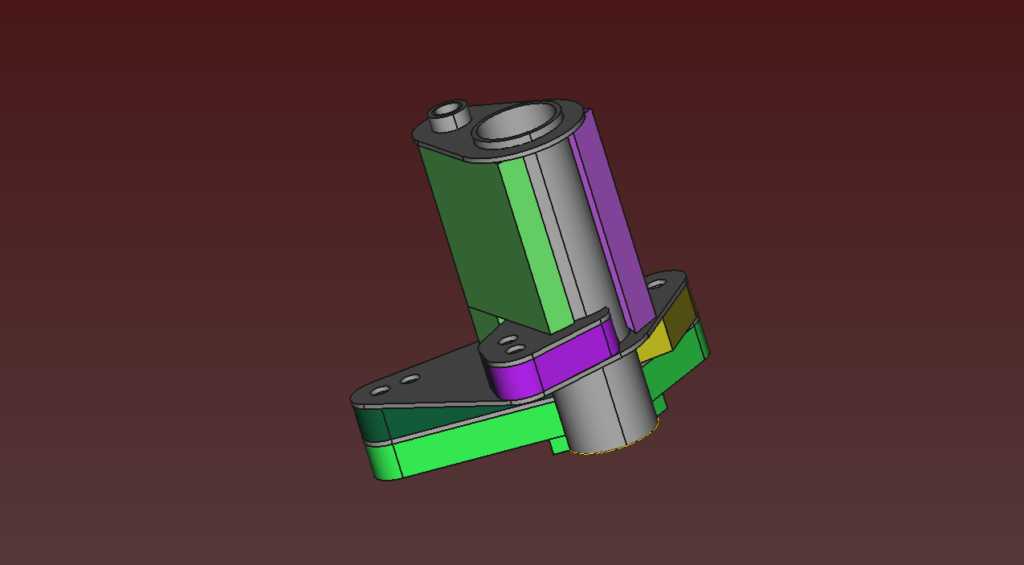
Small parts with lots of heat are there own sort of tricky. Distortion from heat is a constant challenge with welding and can be mitigated by good jigging and heat control. After welding, the part can also be straightened if needed.
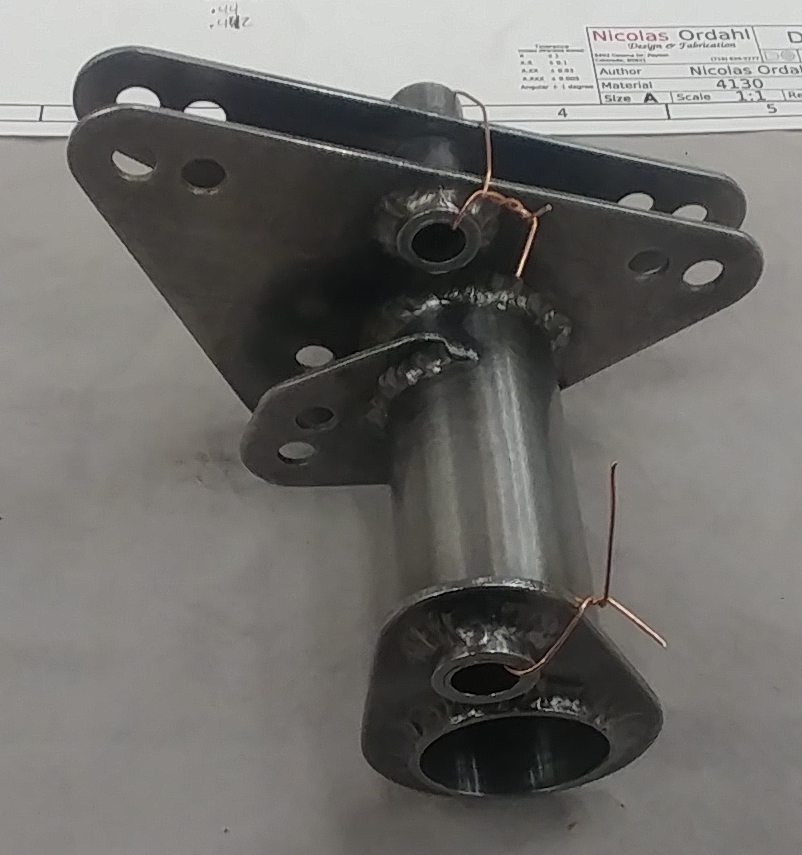
We are proud of this part and the mechanisms we used to meet the tight tolerances requested. 3D printing is a game changer in so many ways, building purpose specific jigs being just one.
Leave a Reply